Professional Online Portfolio
443-852-4675
FireHawk: Morphing Aircraft for Firefighting Applications
Objective
Determine if a morphing aircraft designed to fly consecutive air attack and smoke jumper missions outperforms a baseline aircraft
Air Attack Mission
Identifies target areas and coordinates aircraft for fire suppression

Beechcraft King Air 200
Mission Critical Considerations: Endurance, Field-of-View, Communication
Smoke Jumper Mission
Drops firefighters and cargo into active wildfire situations

Mission Critical Considerations:
Takeoff Performance, C.o.G Shift, Payload
Short Sherpa C-23
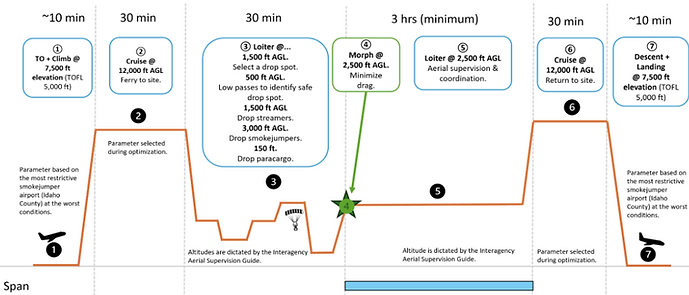
Mission Definition
-
The takeoff and and descent runway distance is determined using a worst case scenario.
-
The runway length of 5,000 ft was decided based on the distance needed to take off of Idaho County Airport (which has the shortest runway for fire operations), and on the hottest summer day in the area.
-
This is because airplanes need more distance to takeoff at higher temperatures and less dense air.
-
Smokejumper operations follow, where altitudes are prescribed by the Interagency Aerial Supervision Guide. Span increases after dropping off smokejumpers and paracargo.
-
The FireHawk can still loiter for 3 hours minimum if smokejumpers and paracargo cannot be dropped off due to bad jumping conditions.
Fulfilled System Requirements


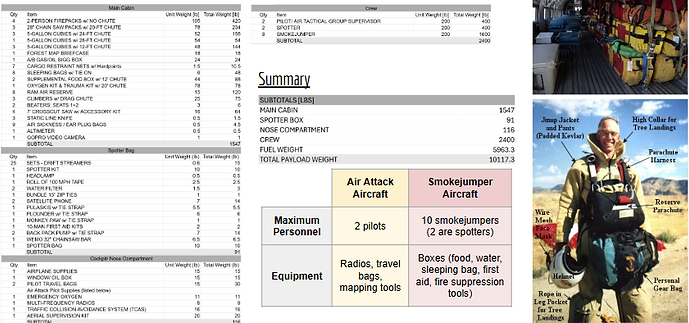
Payloads
-
The detailed payload breakdown includes all the necessary equipment for 2 air attack pilots and 10 smokejumpers.
-
The FireHawk can hold the number of supplies required by 8 jumpers, such as 3 chainsaws, water cubies, 8 sleeping bags, etc. They are usually sent down in paracargo boxes .
-
It can hold enough supplies for 2 spotters (spotters also count as smokejumpers who don’t jump), such as 25 streamers, 1 kit, 1 headlamp, etc.
-
It can hold the number of supplies required by 2 air attack pilots, such as 2 travel bags, 1 tank of oxygen, 1 supervision kit, etc.
-
This payload weight has been considered in the overall design and CG calculations. In summary, the payload (equipment, 12-member crew, and fuel) weighs about 10,000 lb.
Technical Approach
-
We first started by defining our combined smokejumper and air attack mission. We spoke to industry professionals and did extensive research to determine the mission requirements that would inform our design.
-
Next, we used Raymer’s Aircraft Design methods and other physics-based models to develop a custom sizing and performance tool. This tool accepted geometric inputs and calculated weights, sizing, stability and control parameters, and structural components. Much of our work went into refining this tool as our assumptions got better. Once we deemed this tool acceptable, we used it to size our baseline aircraft.
-
This baseline could fly the same mission we were sizing our morphing one for, but did not incur a weight penalty for morphing. We also researched morphing technologies to pick the most optimal, then incorporated these technologies into our model.
-
Then we could compare the sized morphing and non-morphing aircrafts to determine if we received a large enough benefit from the morphing configuration. This determined our feasibility study result.

Compareable Aircraft
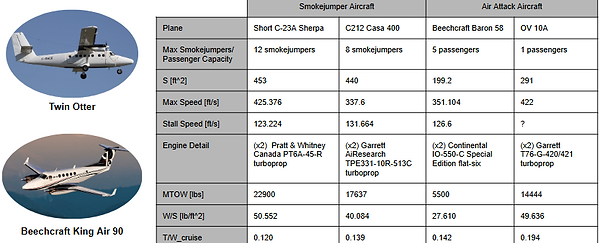

Morphing Technology Comparisons
Generally, morphing mechanisms:
-
Increase weight / decrease payload capacity
-
Heavier with added mechanisms
-
Reduction in allowable payload
-
-
Decrease drag
-
Adaptation to different flight conditions
-
-
Increase lift
-
Adjustment of aerodynamic surfaces
-
-
Reduce structural robustness
-
Dynamic load changes
-
Fatigue from moving parts
-
Weakness at integration points
-
Engine Selection
-
Selected engine: PW127G
-
Can only be installed with 6-blade propellor
-
-
1 engine
-
Total thrust: ~2731 lbf
-
Total weight: 1067 lbm
-
-
2 engines
-
Total thrust: ~5462 lbf
-
Total weight: 2134 lbm
-




Propeller Selection
Dowty has better performance but the difference is quite minimal and the Hamilton Sundstrand performs better in rugged conditions, so the Hamilton Sundstrand propellers was selected for our aircraft
Longitudinal Center of Gravity
-
An analysis of the empty weight center-of-gravity was conducted via a component build-up.
-
Major subsystems were simplified as point masses at a longitudinal location from the nose of the aircraft.
-
This produced an empty CoG that was then used for stability and control estimates.
-
Furthermore, the empty CoG was used to position the wing properly in the longitudinal direction, so that the aircraft’s static margin was within an acceptable range.


Center-of-Gravity Envelope
-
This graph shows the range that the center of gravity of the aircraft changes during a typical mission.
-
The primary drivers for CoG shift during the mission are fuel burn and payload drops. Moreover, we accounted for the shift in crew as the smokejumpers prepare to deploy by moving aft in the aircraft.
-
Using this scenario-based analysis, we determined what the most forward and most aft CoG would be during nominal operations.
-
Both extremes were within our allowable range and satisfied the static margin requirement.
-
We wanted the static margin range to be 5% - 25%, based on Raymer’s methods. Ultimately, we found our static margin to range from 8% - 20%.
Stability and Control
-
Initial tail sizing was done for the baseline model and the morphing model using tail volume coefficients from Raymer’s book.
-
The longitudinal stability was confirmed via a moment summation about the y body axis. This ensured the aircraft had at least enough horizontal tail area to control its pitching moments during a worst-case airspeed condition.
-
Similarly, the lateral stability was analyzed with an engine-out method, ensuring the vertical tails had enough surface area to maintain control during an engine-out scenario after take-off.
-
The baseline and the morphing aircraft were deemed to have sufficient stability characteristics. This simple analysis was enough for our feasibility study, but more in-depth stability and control analysis needs to be conducted if this project were to move forward.


Baseline Configuration
-
The configuration resembled that of traditional smokejumper aircraft.
-
A V-tail and high-wing were in place to prevent the smokejumpers from hitting anything on the aircraft as they exit the vehicle.
-
The aircraft is a twin-engine as the smokejumpers like reliability.
-
Finally, the door is mounted far aft of the wing for easy egress, and the aircraft has a ramp to aid in cargo onboarding and delivery.
Morphing Aircraft CAD
-
The morphing aircraft utilizes a high wing and high tail configuration.
-
The main wing features a tapered leading and trailing edge which can extend from 85 to 105 feet.
-
The wing extension works by telescoping through the structure of the main wing.
-
The aircraft features a double fuselage configuration where the left fuselage is dedicated to the pilots, spotters, and cargo while the right fuselage is dedicated smoke jumping operations.
-
Because of the dual fuselage design, bicycle landing gears were selected and engines were placed in the nose of both fuselages to spare structural space within the wings.
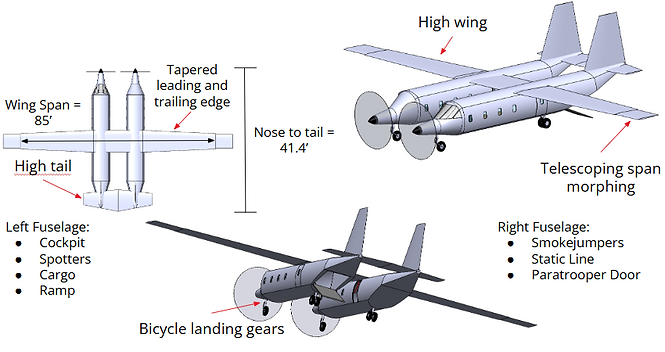

Morphing Aircraft Interior Layout
-
The aircraft meets all regulations set by the Smokejumper Aircraft Screening and Evaluation Subcommittee (SASES) to ensure the safety of the smokejumpers while exiting the aircraft.
-
These requirements include accessories such as anchor cables for the smokejumpers to hitch their static lines to, handrails that extend from the middle to up and over the top of the door, a door boot to cover the sharp edges of the door that prevent severing static lines,and an inwards hinging door which must be greater than 25”x36”.
-
There is a required emergency exit door located within 30 feet from the aircrew.
-
The spotters of the aircraft sit behind the pilots and are also responsible for deploying the cargo from the ramp.
-
The floor in both fuselages is palletized to allow cargo to be safely and securely fastened to tie off holes in the floor.
Morphing Aircraft Interior Layout
-
The aircraft complies with FAA regulations which specify 20 inches of clearance to ensure a safe and timely exit of the aircraft incase of an emergency.
-
By knowing the egress path of the aircraft, the cargo storage area couple be determined.
-
Space for the spotters to walk throughout the cabin and spot fires from the view ports could also be determined as well.


Tire Selection
-
With the max weight of the aircraft having been determined to be 31,500 lb, tires could be selected.
-
If weight is distributed among 4 main aft wheels, the design load of each tire is approx 7,900 lb given the design factor of 1.07.
-
Raymer gives an equation on what size a wheel should be based on the design load. The selected tire is the Michelin 029-616-0, it roughly matches these dimensions and also can handle the design load.
Wheel Layout
-
The wheels are in a bicycle configuration on each fuselage, Michelin wheels are used for the nose and aft main wheels.
-
The nose gear wheel location is restricted by where there is space for it to retract.
-
The aft main wheels are located such that they hold about 90% of the aircraft weight, as is typical according to Raymer’s book.
-
The calculation for worst case loading on the main gear and nose gear was calculated via a method in Raymer’s book. (These are separate cases of loading, so they don’t add up to 100% of aircraft weight.)
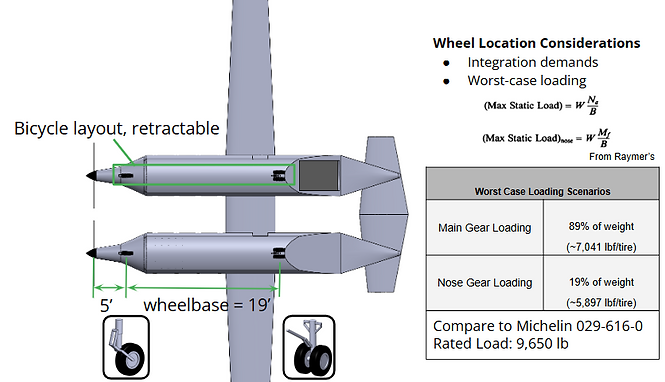

Detailed Wing
-
The detailed wing was designed to meet initial assumptions used in aircraft sizing and to pass structural analysis
-
Airfoil was chosen to satisfy a maximum lift coefficient of 1.60
-
Added benefit of the NACA 6412 is that it maintains fairly low values of drag coefficient for a large range of angles of attack.
Spar Sizing
-
Max wing deflection of 16.5 in
-
Within acceptable deflection of 51 in
-
-
Max bending stress of 19278 psi
-
Within max yield strength of 73000 psi
-
-
Max shear stress of 18041 psi
-
Within allowable shear strength of 43800 psi
-
-
Distance between main and rear spar
-
At root: 64.8 in
-
At tip: 45.4 in
-


Wing Structural Analysis
-
Maximum stress occurs near the root of the wing, as expected. Neither of the estimated theoretical maximum bending stress or the FEA results show yielding of the wing.
-
The wing will yield first due to buckling (critical buckling stress = 21160 psi) before it reaches its yield strength. Therefore, the factory of safety is ~1.5
Performance Metrics
-
All performance metrics were pulled from predictions in our team's Jet Sizer system model, and all met or exceeded all goals set.
-
For takeoff, the aircraft is able to achieve a ground roll of 3180 ft at an altitude of 7500 ft. This was to ensure that FireHawk could takeoff from all smokejumper base airports on their highest-temperature days.
-
Cruise is completed to the fire sight at near max throttle, achieving a max speed of 300 kts and L/D of 16.6. The aircraft is able to carry enough fuel for operations 400 nmi away from the home airport, with a loiter time of 4 hours after payload drop.


Morphing vs. Baseline
-
The biggest question from the beginning of the project was to see if an aircraft performing this mission receives any benefit from a morphing mechanism.
-
To ensure that we are comparing apples to apples, a study was conducted which varied the span of the aircraft either by changing the baseline span or by having a base span that morphed to the desired length.
-
Because the weight of the actuation method was unknown, it was lumped into the weight of the additional portion of the wing as a weight per area coefficient.
-
From our studies done, it can be seen that the aerodynamic benefits of morphing per flight segment outweighed the weight penalty for nearly all extension values as long as the weight coefficient was under 20 lbs/ft^2.
Future Work and Considerations
-
All performance metrics were pulled from predictions in our team's Jet Sizer system model, and all met or exceeded all goals set.
-
For takeoff, the aircraft is able to achieve a ground roll of 3180 ft at an altitude of 7500 ft. This was to ensure that FireHawk could takeoff from all smokejumper base airports on their highest-temperature days.
-
Cruise is completed to the fire sight at near max throttle, achieving a max speed of 300 kts and L/D of 16.6. The aircraft is able to carry enough fuel for operations 400 nmi away from the home airport, with a loiter time of 4 hours after payload drop.
